在汽车、3C电子等制造领域,工业机器人已实现简单重复工序的规模化应用。然而面对高复杂度、非结构化装配场景,仍存在大量人工操作环节。机器人若要真正替代人工,除了高精度运动控制外,还需要具备人手般的柔顺操作能力,关节力控技术就是其中的核心所在。
现阶段协作机器人力控装配,大多采用基于电流环控制或外置力传感器的末端力控方案,在实际场景应用中仍面临诸多弊端与痛点。
▍场景痛点
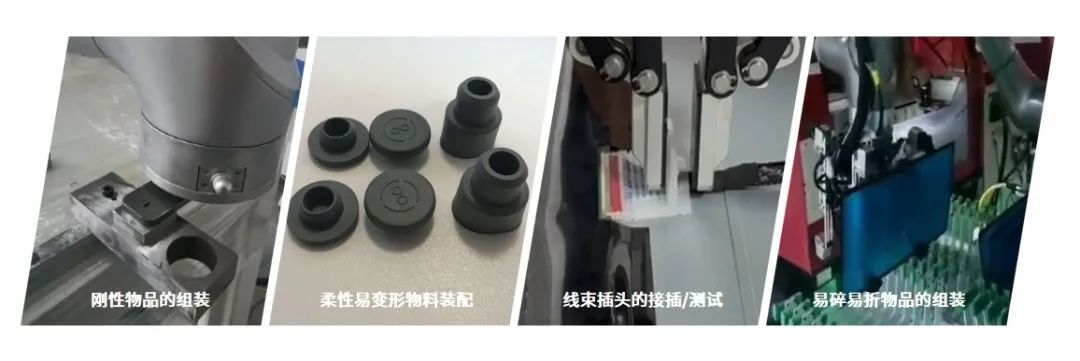
■ 装配良品率低
一方面,装配精度要求高,而来料一致性差,柔性且易变形的工件易导致装配误差;另一方面,柔性线路板及多自由度线束在插装或检测时,视觉系统引导精度不足容易导致装配失败;此外,易碎产品在组装过程中存在损坏风险。
■ 生产节拍不佳
末端力传感器装配方案,传感器到手臂的控制时延较长,操作动作慢,难以满足节拍要求。
■ 调试部署周期长
需要在不同硬件之间反复调参,周边非标硬件较多,调试复杂。
■ 智能自适应挑战
对于高精度、长序列装配任务,需要机器人能够自适应兼容多品类制造工艺,以降低产线换型改造的周期与成本,对机器人环境感知与智能决策能力提出要求。
▍解决方案
珞石机器人深耕装配场景,持续优化装配工艺,凭借业内领先的柔性力控技术、基于全关节力控的柔性协作机器人产品体系,以及结合实际场景的人工智能技术,精准解决用户痛点,为制造业装配场景打造出一条兼具经济性、易用性和可靠性的柔性智造升级路径。
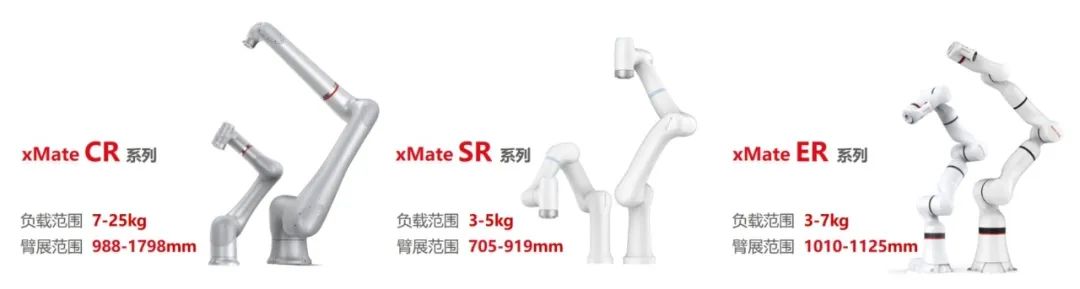
全关节力控的柔性协作机器人产品
1 针对来料一致性差、工件柔性易变形、视觉引导精度不足、产品易碎易损坏等因素导致良品率难以提升的问题,珞石:
1)打造“视觉伺服+力控搜索+柔顺装配”解决方案,将装配成功率提升至99.5%以上
珞石力控搜索规划技术,能够敏锐感知并灵活调节接触力,确保装配动作精准无误的同时具备柔性调整能力。
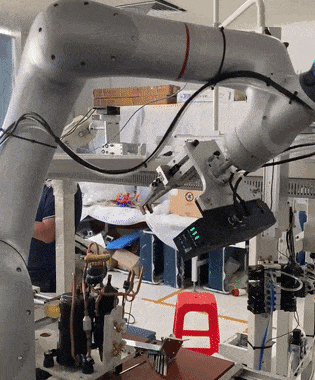
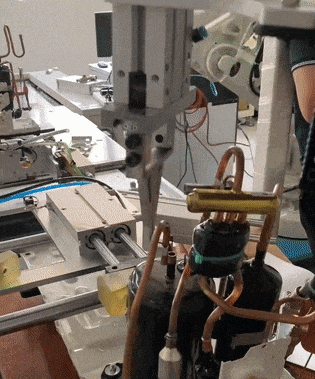
以空调管口装配场景为例,需依次完成压缩机与冷凝器的管口配管,配管深度大于10mm,要求机器人配管一次合格率≥99%,搜索时间≤3S。由于是紧配合安装,过程中极易卡住,很难达到10mm的配管深度,难以满足合格率要求。且装配复杂,仅依赖3D视觉难以保证精度。
2台珞石CR18柔性协作机器人协同工作,采用柔顺控制算法,结合力控搜索规划技术,在视觉偏差较大的情况下也能精准完成配管。机器人具备自主判别空插状态的能力,通过参数自适应调整使一次合格率提升至99.9%,节拍压缩至14秒。
2)通过限制装配力阈值设定,实现0.5N的产品保护
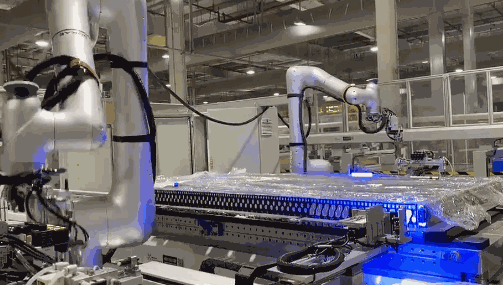
在电池连接片装配场景中,塑料支架卡扣装配时极易损坏,导致外观损伤、变形或连接片脱落。
2台珞石CR12柔性协作机器人协同作业,装配时,机器人开启力控功能和变刚度阻抗模式,实时控制末端受力,当受力大于设定阈值时,机器人停止装配,记录异常数据并告知PLC具体位置,有效避免安装过程中对工件的损坏,保护精密零件。
2 针对装配节拍不理想的问题,珞石采取如下措施:
1)“手眼配合+力控”实现智能装配,搜索时间缩短至1s
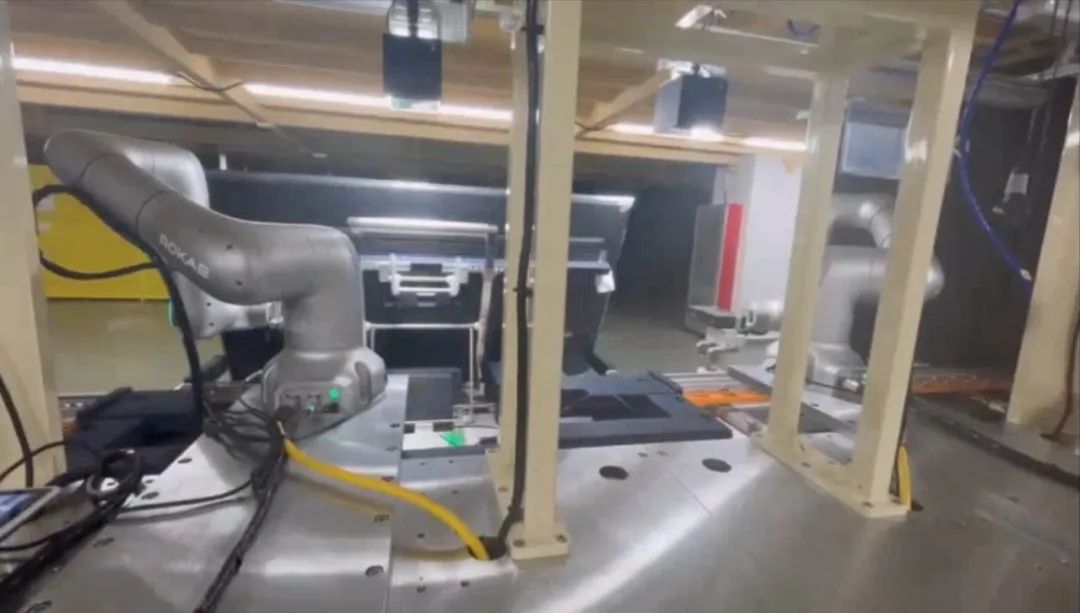
在电视机出厂通讯检测环节,每台电视机都需接入电源线与HDMI线来完成检测,配合公差要求±0.1mm,工序节拍要求控制在14 秒以内。传统视觉+机器人方案难以保证精度和节拍要求,插拔易失败还可能损坏产品,加之电视机型号众多,适配困难。
2台珞石机器人协同作业,搭配同步运行的视觉系统,分别负责插入电源线和HDMI线。机器人插入公头时开启柔顺浮动功能,借助力控搜索规划技术,搜索时间缩短至1s。在插拔过程中实时感知受力情况,既提高插入成功率,又避免损伤设备与产品。该“手眼配合+力控”方案不仅能确保±0.1mm公差的高精度装配,还满足了12秒/台的严苛节拍要求,可适配50/55/65/75寸多种电视机机型。
2)全关节力控,高动态响应,快速实现装配
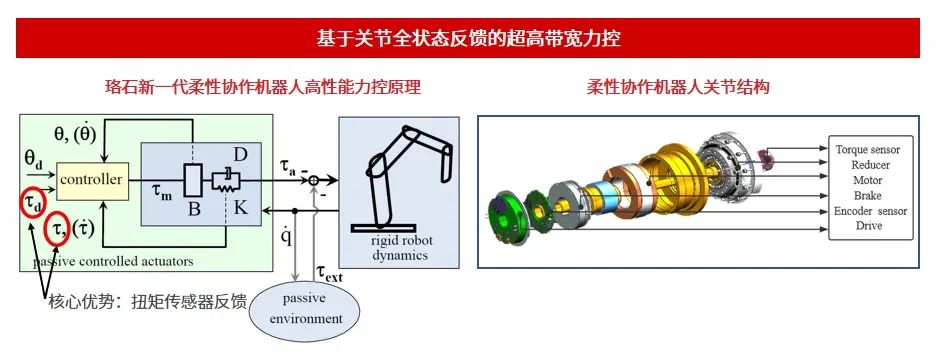
基于关节全状态反馈的高带宽力控
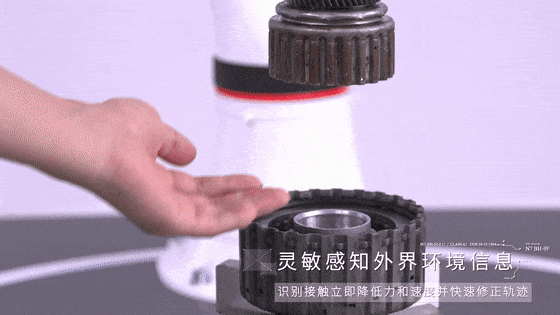
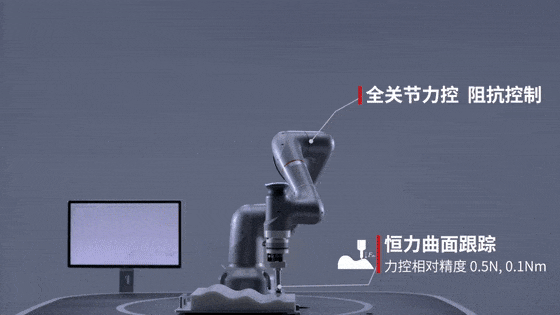
珞石柔性协作机器人全关节集成力控,通过在每轴关节内置高精度力矩传感器,在不增加硬件成本的前提下,同步实现高精度运动控制和柔顺力控操作能力,力矩测量分辨率优于0.1Nm,关节力控闭环频率>10kHz,力控带宽更高,响应速度更快。相对于传统末端力控,力控任务效率可提升3倍以上,有效应对产线波动及工艺误差。
3 针对调试部署周期长的问题,珞石:
1)完整力控工艺包,快速设置工艺参数
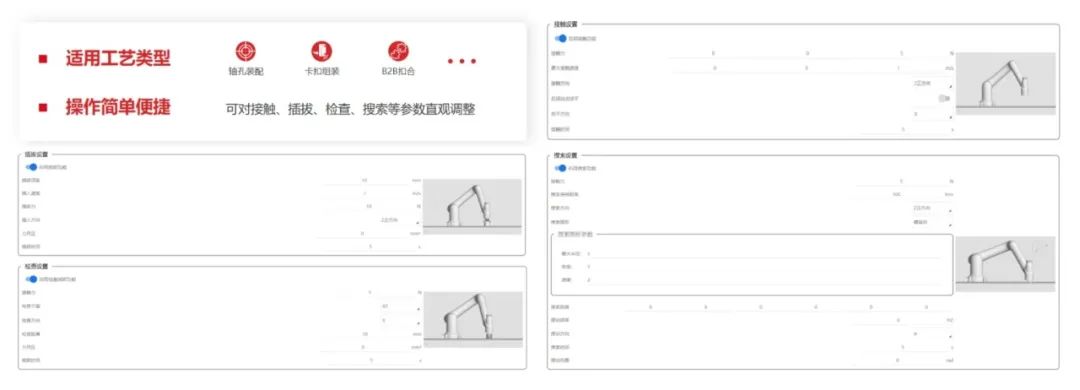
操作简单,可对接触、插拔、检查、搜索等参数进行直观快速调整,缩短调试时间,提升装配效率。
一键部署,适用于轴孔装配、卡扣组装、B2B扣合等工艺类型,无需额外力控传感器,显著降低应用拓展成本。
2)拖动示教功能,快速规划任务轨迹
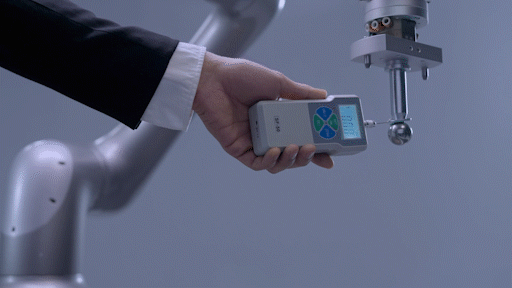

基于关节力控的柔顺拖动示教
基于关节扭力闭环主动控制,珞石柔性协作机器人可实现柔顺拖动示教,仅需1N以内的拖动力即可轻松进行精准拖动,实现复杂点位和连续轨迹的直接示教,大幅提升示教效率的同时,降低拖动不平顺带来的示教碰撞风险,零”门槛使用机器人。
4 针对复杂装配场景,机器人无法智能自适应工艺的问题,珞石:
1)深度融合“机器人+AI”,构建具身智能柔性装配场景
珞石积极在“机器人+AI”领域进行布局,通过将人工智能技术、具身智能引擎以及大模型训练技术深度融合,自主研发出全新的具身智能双臂机器人,其具备自主任务分解能力、实时决策能力和毫米级高精度操作性能,能够针对不同应用场景切实打造出解决实际问题的具身智能产业化落地方案。
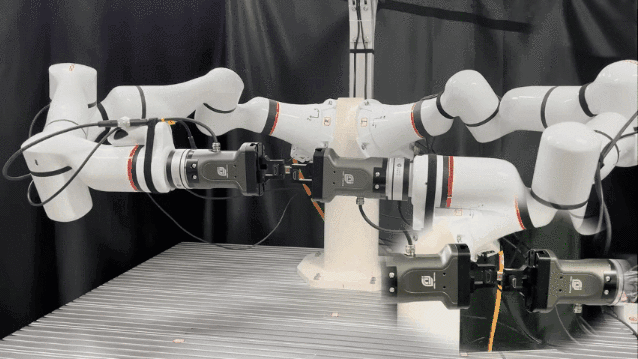
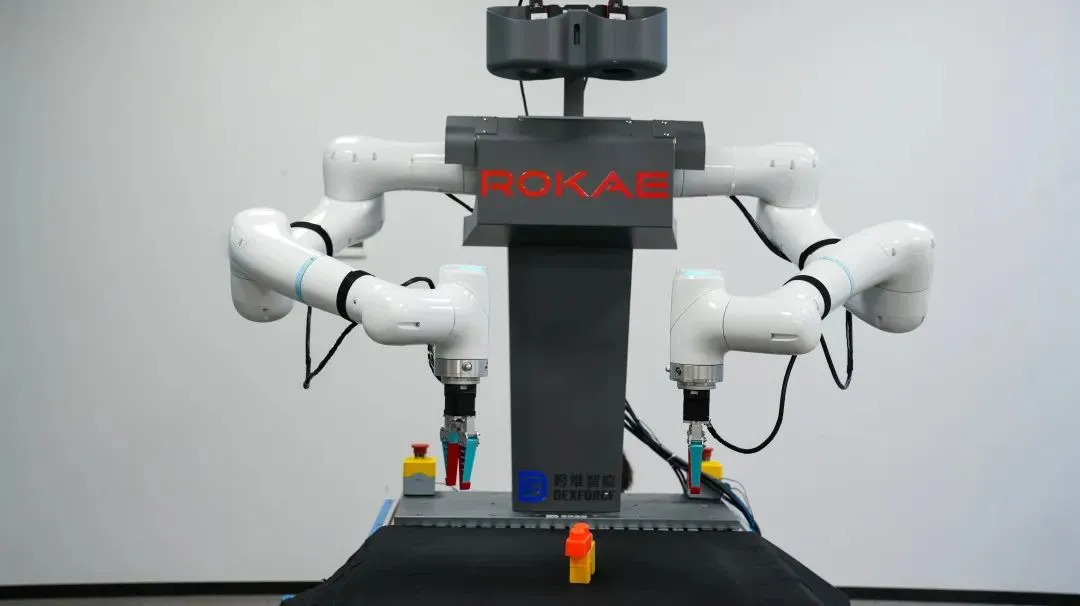
珞石具身智能双臂机器人装配演示
具体到具身智能双臂机器人的智能化装配场景,借助先进的底层算法、智能视觉、深度学习及模型训练技术,珞石具身智能双臂机器人能够高效完成一系列高精度、长序列的装配任务,如服务器机箱的存储器插拔、CPU装配、线束界面检测与插拔等,实现完整的智能化装配应用。
▍应用案例
针对客户的具体需求和难点,珞石机器人凭借在力控领域领先的行业实力和创新能力,提供高效柔性的机器人力控装配解决方案,已在众多场景落地应用。
■ 发动机VVT相位器装配
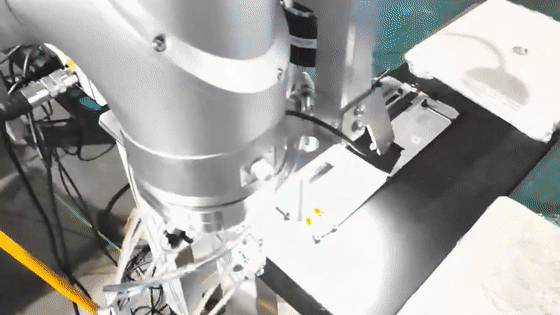
■ 新能源汽车自动充电/检测
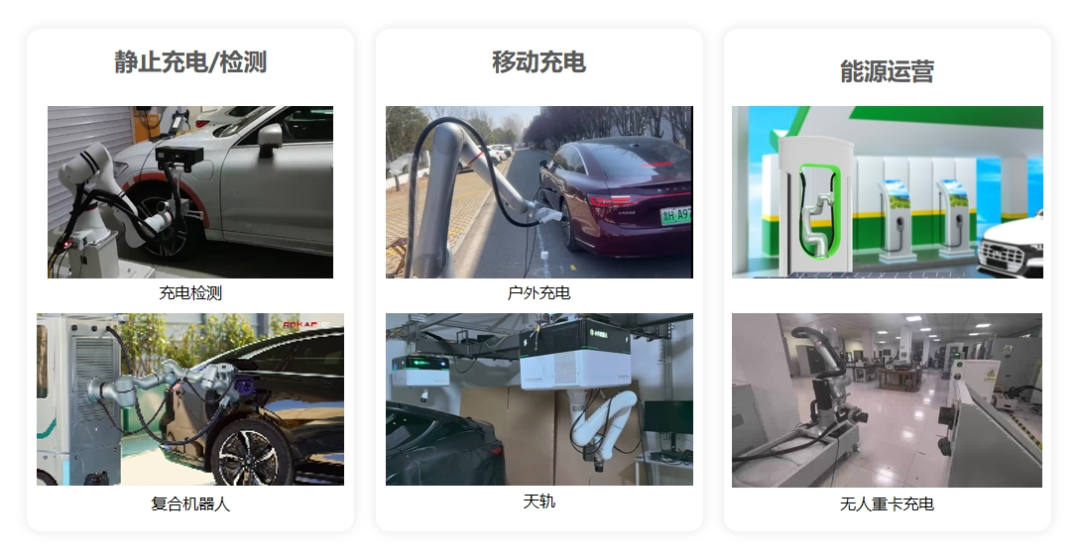
■ 通用场景(大扭矩拧紧/贴合涂胶等)
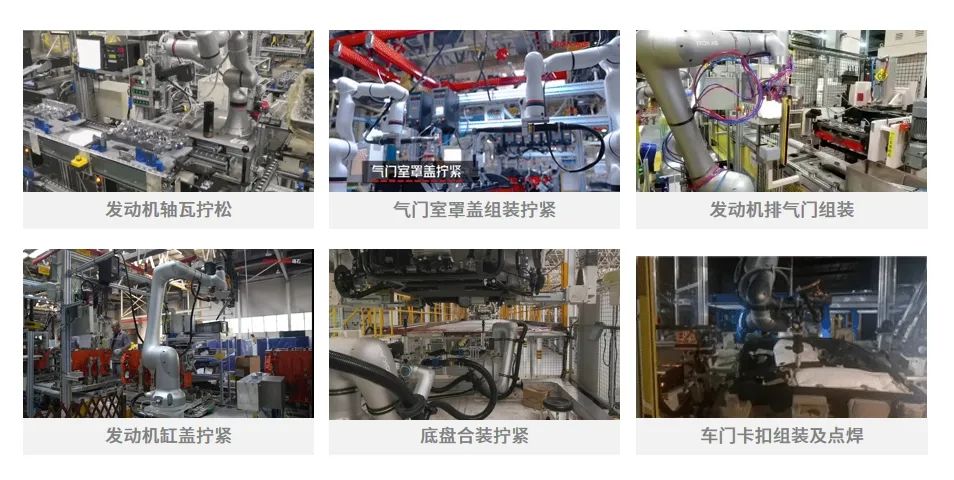
(文:机器人大讲堂)