当前,全球制造业正面临人口结构变化与成本上升带来的转型压力。作为新质生产力的重要载体,人形机器人被赋予支撑经济高质量发展的战略意义,并被视为技术竞争的关键领域、产业革新的前沿赛道及经济增长的新兴动能,其潜在价值受到广泛关注。
行业观察显示,尽管近年来人形机器人领域资本投入持续增长,技术迭代不断加速,但外界质疑声始终伴随。有观点指出,该领域长期存在“实验室技术转化难”与”工业场景落地慢”的割裂现象,引发关于技术应用边界的争议:人形机器人究竟能创造何种实际价值?其替代人工的可行性及时间表是否明确?甚至有人直言,部分产品仍未突破技术演示阶段,距离产生实质性经济效益尚需时日。
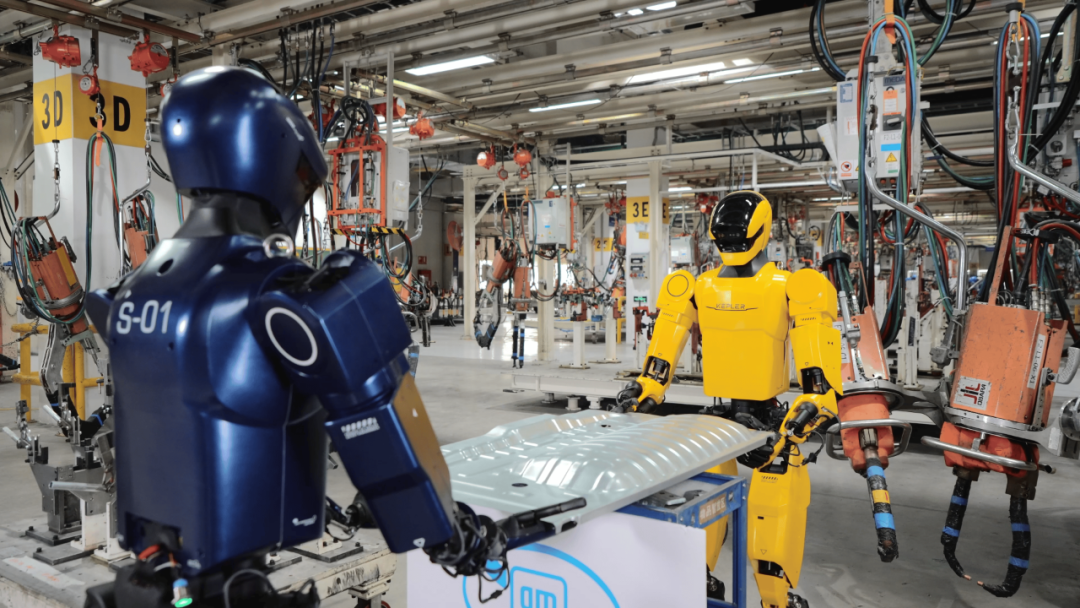
在此背景下,上海开普勒机器人有限公司在上汽通用汽车完成实景实训,引发行业关注。通过在实际汽车制造场景中开展多轮实测,双方联合验证了开普勒K2“大黄蜂”在复杂工业环境下的作业能力。相关数据显示,开普勒K2“大黄蜂”量采基础版仅需3万美元,可在8小时工作制下替代1.5名工人的效能,在长三角制造业的测算中,其投资回报周期可控制在1.5至1.8年间,后期运营成本显著降低。此次实践不仅回应了行业对于技术实用性的质疑,更标志着人形机器人从概念验证向产业应用的实质性跨越,揭示出中国智能制造在“工业4.0″全球竞赛中把握弯道超车机遇的积极信号。
▍破解两大核心瓶颈,锻造双峰工业适配力
人形机器人要胜任工业场景,必须突破两大核心瓶颈:动力系统的工业级适配性与操作精度的类人化表达。
以打造人形行业领先落地的蓝领人形机器人为目标,开普勒聚焦实用型工业机器人,通过革命性技术架构,构建起其K2“大黄蜂”适配复杂工业需求的“双峰”能力体系。该体系以动力适配、操作精度、群体协作为核心突破点,在上汽通用的实测中展现出显著技术优势。
-
动力系统创新:达成工业级续航与超强负载能力
工业场景对机器人的续航与负载能力提出了极为严苛的要求。开普勒K2“大黄蜂”凭借创新的”串并联结构”设计 与 自研的行星滚柱丝杠执行器相结合,实现双臂30kg的强劲负载能力和长达8小时的续航能力,并能精准执行毫米级精细操作。
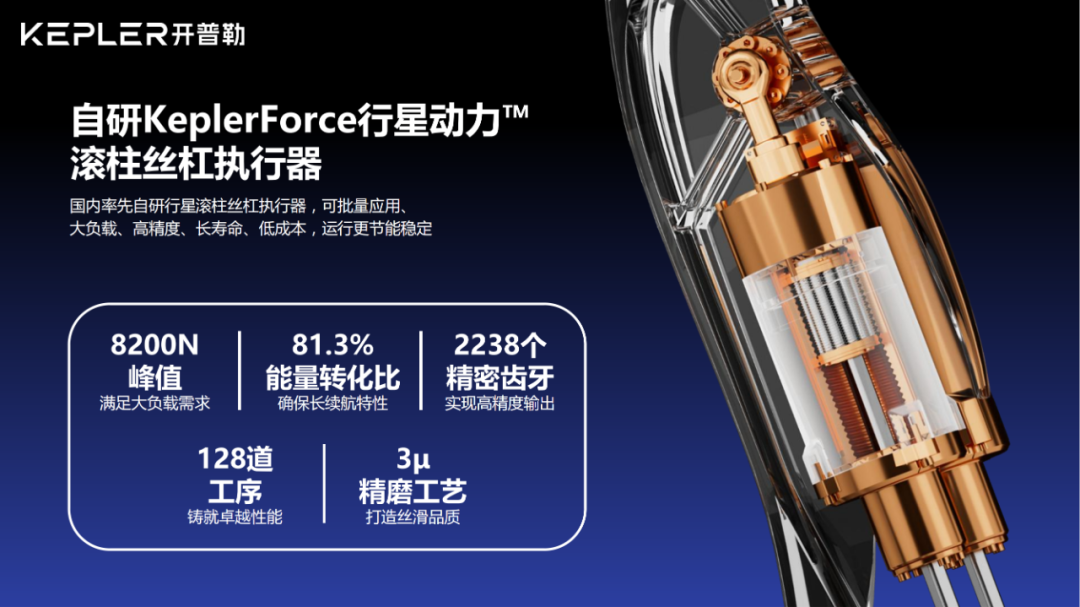
其滚柱丝杠执行器历经128道精密工艺制造,配备2238个精密齿牙,通过行星齿轮系实现旋转运动向直线运动的高效转化,动力传输效率大幅提升,峰值推力达8200N,能量转化效率达81.3%。旋转执行器自研率达85%,采用高扭矩电机与智能算法协同控制,峰值扭矩220N·m,重复定位精度0.01度,可支持毫米级精密操作。
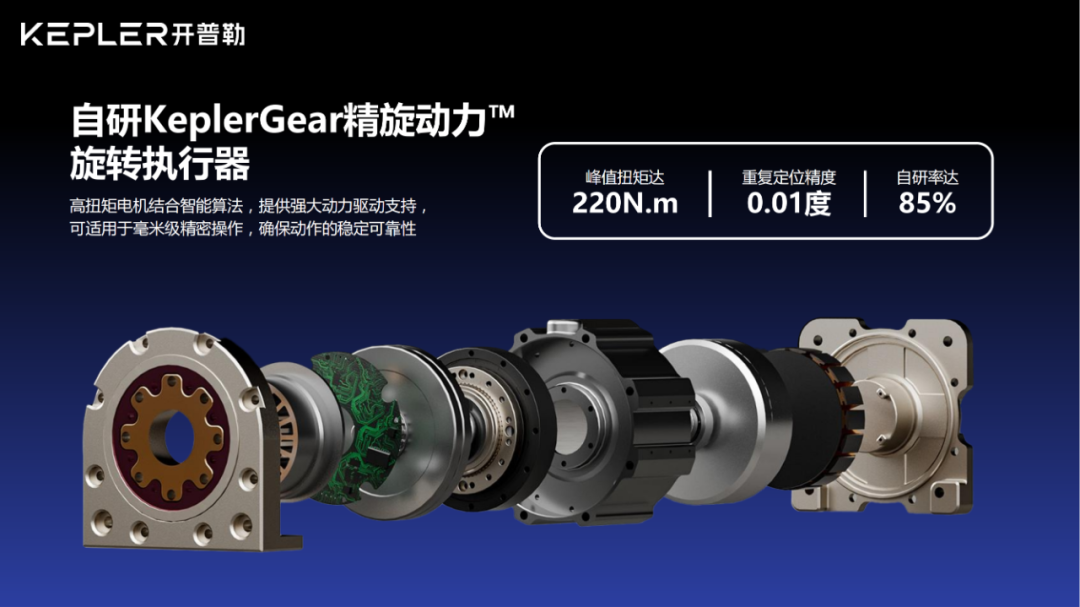
在续航优化方面,开普勒K2“大黄蜂”通过动力结构、控制算法与低能耗设计的协同创新,结合小导程节能方案与智能监测算法,实现“充电1小时,连续作业8小时”的工业级续航能力。机器人静止时关节自锁稳定性达IP65防护标准,自研控制算法可实时监测关节状态,智能调度“无电自锁”与任务执行时序,在保障作业效率的同时最大化延长续航时间。
在负载能力上,开普勒K2“大黄蜂”双臂协同可搬运30kg工件,单手可精准操作15kg物料并实现毫米级定位。这种“大负载 + 长续航”的技术组合,有效解决了汽车制造等工业场景“两班倒”生产节奏下的动力适配难题。
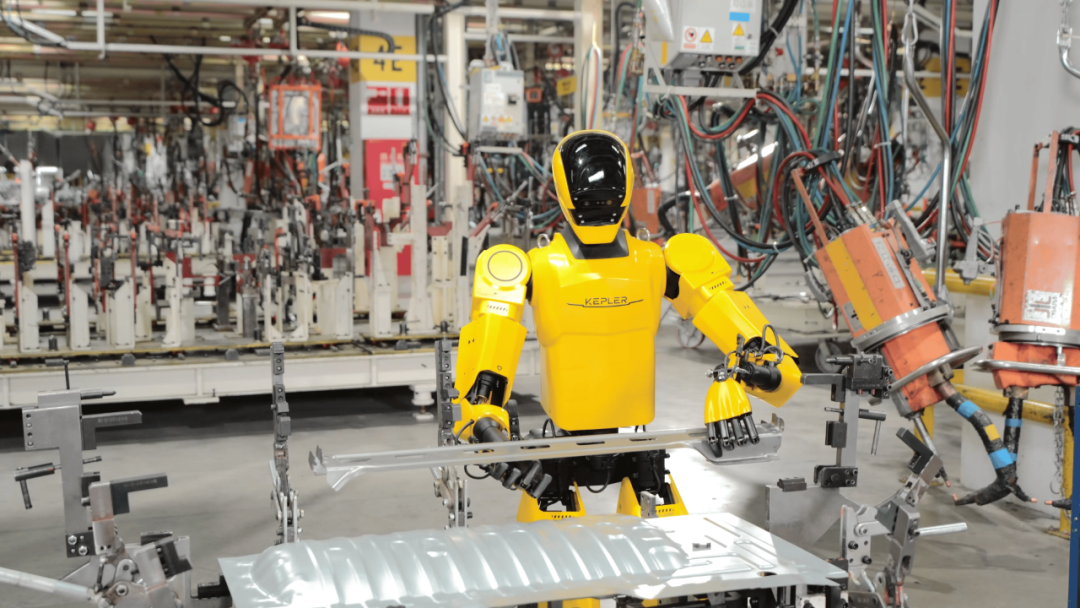
-
操作精度升级:实现毫米级定位与三维质量感知
在汽车制造领域,许多关键工序都依赖工人的触觉反馈和即时判断能力。针对工业精细操作需求,开普勒K2“大黄蜂”配备了自研NimbleMaster灵巧手与六维力感知手腕系统。其灵巧手采用11自由度类人机械设计,单指实现了25点位微力控制,结合六维力感知技术,可实时反馈接触面压力分布。

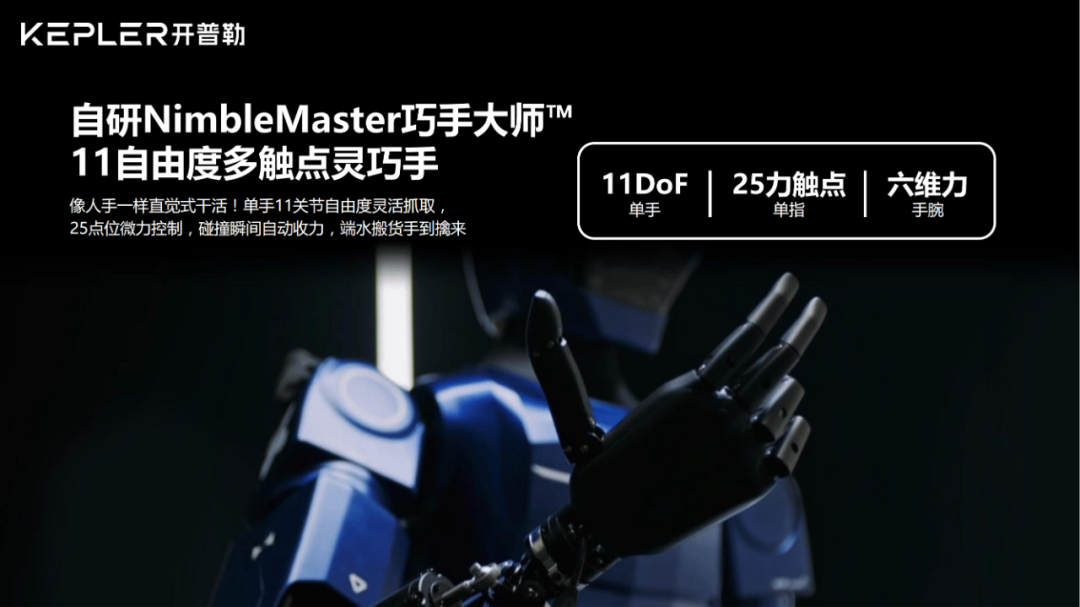
在上汽通用实测中,开普勒K2“大黄蜂”成功完成车身缝隙检测任务,精准控制检测设备操作力度与角度,避免损伤精密仪器,同时自主调节按压力度确保测量精度。在金属冲压件上料应用中,开普勒K2“大黄蜂”展现出毫米级定位精度,可稳定抓取不规则工件并精准放置于作业台,为后续工序提供可靠物料供给。这种“粗中有细”的作业能力,有效解决了工业场景“力控”与“灵活”难以兼顾的技术矛盾。
-
协作模式革新:构建群体智能协同体系
汽车制造中的大型总成搬运等工序需要多人协作。开普勒机器人突破单体智能局限,实现“单体智能”向“群体协同”的范式转变,使开普勒K2“大黄蜂”具备了替代人工班组的潜力。
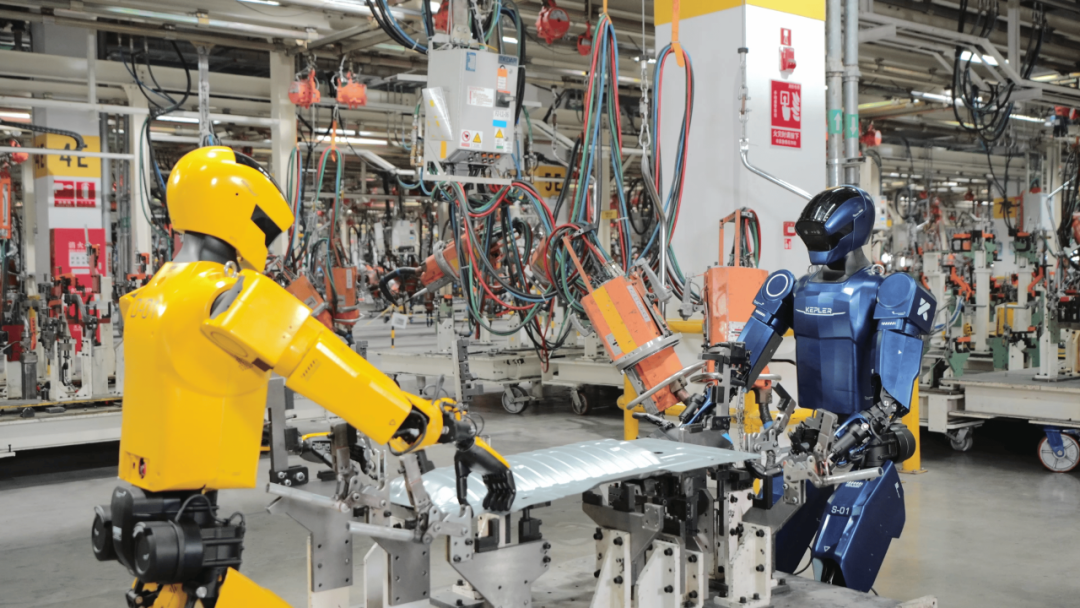
针对超大尺寸金属部件搬运需求,开普勒K2“大黄蜂”通过感知协同与任务分配技术,实现多机同步举升、搬运与定位操作。该能力基于自研KeplerBrain类脑系统构建,采用分层架构实现任务智能拆解,驱动机器人从环境感知到动作执行的全闭环控制。系统集成的多模态融合算法,可综合处理语音、视觉与触觉反馈信息,显著提升机器人在复杂工业环境中的认知与适应能力。
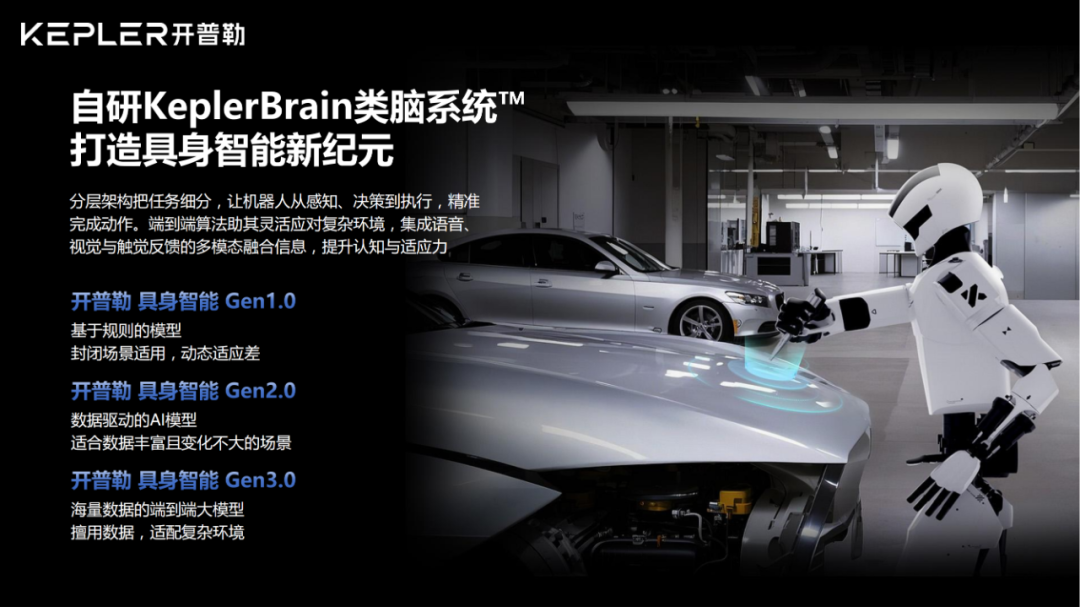
这种群体协同作业能力使开普勒K2“大黄蜂”在应对超大负载与超长工件时展现出高度智能化的执行效率,标志着智能制造自动化水平的重要突破。通过动力系统、操作精度与协作模式的协同创新,开普勒机器人成功构建了适应现代工业需求的人形机器人技术体系。
▍抢占产业应用高地,实现人形机器人中国突围
目前,全球人形机器人赛道呈现出“东升西渐”的发展格局。尽管马斯克引发了人形机器人热潮,但近年来,人形机器人的发展态势已从特斯拉、波士顿动力主导,逐渐转变为中国人形机器人行业初创企业竞相实现技术突破并占据行业焦点。
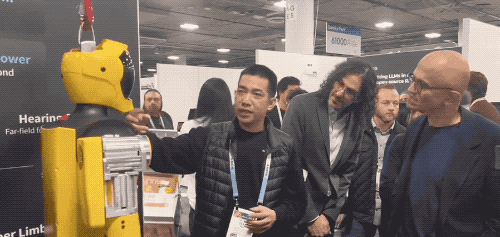
开普勒便是其中的典型代表。2024年,开普勒首次亮相CES便受到微软CEO萨提亚·纳德拉的重点关注,其展示的自研力触觉灵巧手能力,还得到全球人形机器人领军企业Figure的CEO Brett Adcock在X主页上的推荐。当下,在人形机器人应用方面,开普勒更是率先实现了工业级落地突破。
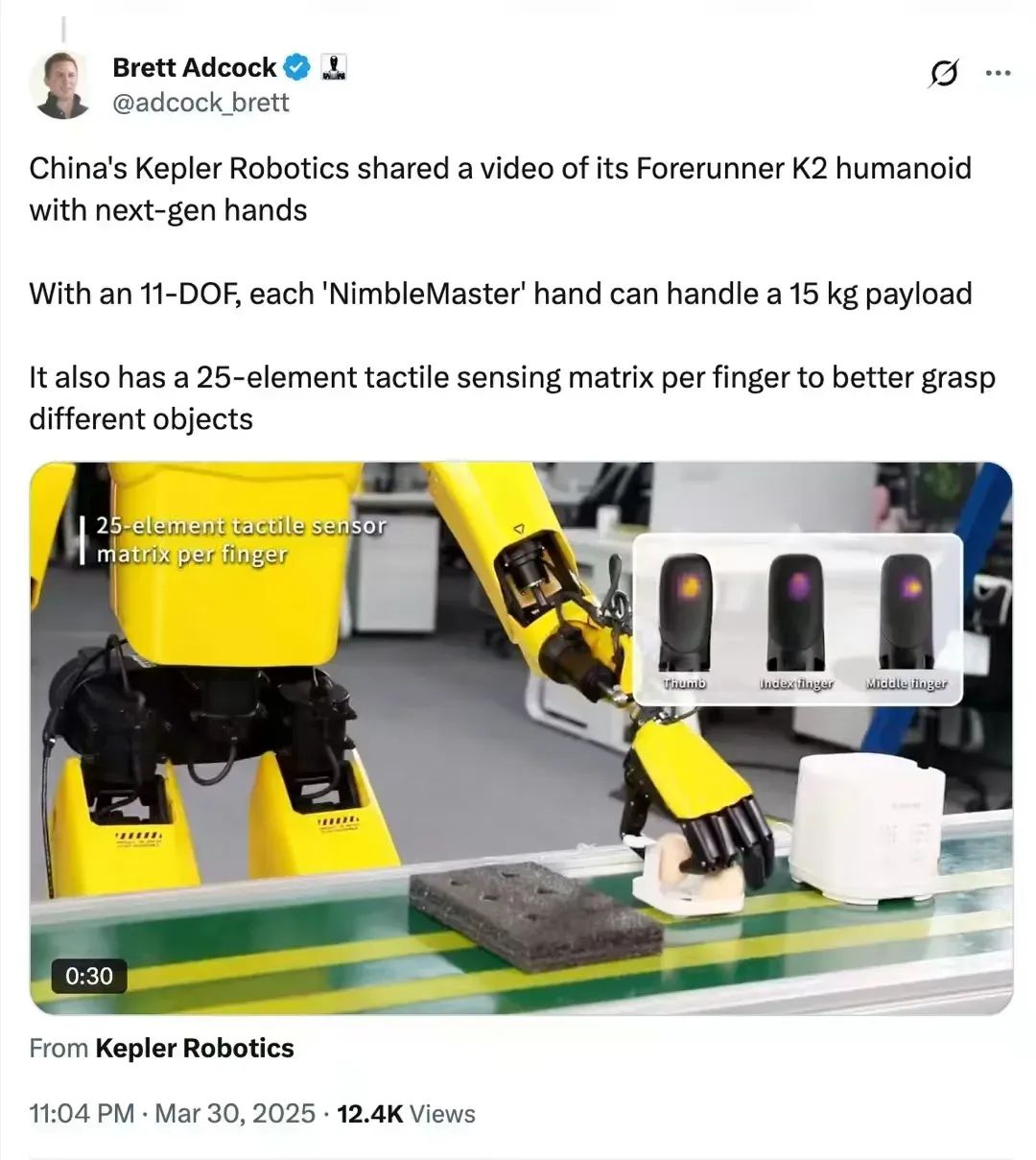
纵观全球人形机器人应用的整体情况,特斯拉Optimus虽以全场景覆盖为目标,但其技术路线侧重于算法通用性,导致在工业场景适配时成本高昂。与之相比,开普勒K2“大黄蜂”的“工厂优先”策略更符合中国制造转型的需求。在开普勒K2“大黄蜂”的研发过程中,开普勒走访了近50家目标客户企业,全面了解不同行业的需求与痛点,调研了智能制造、仓储物流、特种行业、科研教育等领域的大量实际场景,对机器人的技能进行归纳和分类,最终将“实用性”与“经济性”深度融合。其人形机器人产品不仅具备稳定的工业作业能力,更凭借出色的成本效益,成为真正可规模部署的智能劳动力解决方案。
而开普勒能取得这样的成果,得益于其在技术和供应链方面的优势。凭借自有核心技术和80%核心零部件自研自制的高自研率,以及本地化部件采购的供应链优势,开普勒也实现了高工程化和量产能力,其成本控制处于全球领先水平。
值得一提的是,中国拥有全球最完整的汽车、3C、新能源产业链,这为开普勒K2“大黄蜂”提供了海量测试场景,进一步助力开普勒在人形机器人应用领域的发展。综合来看,开普勒无疑将成为蓝领人形机器人落地的先行者。此次开普勒与上汽通用的合作,不仅验证了开普勒K2“大黄蜂”的工业可用性,还建立起“场景实验室”模式。该模式允许机器人企业在真实生产环境中迭代技术,加速技术成熟周期。
随着技术日益成熟和人形机器人成本不断下降,预计未来3 – 5年内,人形机器人有望替代汽车制造中40%的重复性工种,推动制造业人力资源结构向“技术密集型”转型。在这一全球制造业“机器换人”的历史性拐点时,以开普勒为代表的企业构建的不仅是机器人本体,更是中国智造的话语权。这场从实验室到生产线的征程,终将重新定义人类与机器的合作边界,开启一个属于工业元宇宙的新纪元。
(文:机器人大讲堂)