连续型机器人作为新一代智能装备,凭借其类生物组织的柔性细长结构和灵巧运动能力,在特种检测、精密装配、微创手术等领域展现出巨大应用前景。
然而,这类机器人因存在强欠驱动特性、非线性动力学等复杂问题,其末端位置与姿态的协同控制(例如象鼻、蛇、鸵鸟等自然生物捕食行为)始终是制约应用落地的技术瓶颈。
图1 自然生物端部的位–姿协同运动行为
▍提出新思路,实现基于动力学的末端位置–姿态协同精准跟踪控制
为克服上述挑战,来自大连理工大学彭海军教授的研究团队对连续型机器人末端运动控制问题展开攻关。立足动力学与最优控制理论,创新性地提出了基于微分–代数方程(DAEs)动力学模型的连续型机器人末端轨迹跟踪瞬时最优控制(IOC)方法,首次实现绳驱张拉连续型机器人末端位置与姿态的协同控制。
实验数据令人印象深刻:该技术使末端位置追踪相对精度高达98.3%以上、姿态角度均方根误差控制在3度以内、平均单步闭环控制速度突破10毫秒大关,总体控制性能指标达到国际领先水平。
该研究论文以“Position and Orientation Tracking Control of a Cable-Driven Tensegrity Continuum Robot”为题发表在机器人领域顶刊《IEEE Transactions on Robotics》上。大连理工大学为论文第一单位,通讯作者为彭海军教授,第一作者为李飞助理研究员。共同作者包括上海交通大学谷国迎教授,大连理工大学王永青教授和杨浩博士生。
▍张拉连续型机器人的结构与驱动一体化创新设计
张拉整体结构(Tensegrity)是由受压构件和受拉绳索组成的自平衡系统。如图2(a)所示,受人体脊柱启发,研究团队设计了一种仿脊柱张拉连续型机器人(TCR),它由若干受压部件(杆、圆环)与受拉绳索(或弹簧)串联组装而成。
这种设计中,锥形刚性构件模拟脊椎骨,柔性绳索模拟肌肉或韧带,通过绳索的收缩与释放实现类似肌肉的牵引功能。在6根主动滑动绳索的驱动下,TCR可实现包括图2(c)所示的J-、S-、I-、C-、O-和L-形等多种变形模式。具有良好的运动灵活性。
图2 TCR结构设计与灵巧运动:(a-b) TCR结构示意图及部件单元,(c) J-, S-, I-, C-, O- 和L-形的构型
图3展示了TCR的制造过程。首先,通过三角形分布的支撑杆与圆环连接形成锥体基本模块;然后,利用3根弹簧连接两个相邻模块构成张拉柔性铰;最后,通过模块化组装,配置滑动绳索驱动系统,获得一个长700mm、直径70mm的两节式TCR结构。
图3 TCR的制造过程:(a) 张拉柔性铰,(b) 装配,(c) TCR的本体结构,(d) 3D打印的样机
这种设计的特点在于,弹簧连接形成的柔性铰降低了部件间的自摩擦(因为刚性部件之间没有直接接触),同时提供了各方向小范围的平移自由度,特别是轴向收缩运动自由度,扩大了机器人的工作空间。
▍面向控制的动力学建模:精准控制的理论基础
精准控制的前提是准确的动力学模型。连续型机器人在运动过程中会受到摩擦、惯性和结构弹性变形等因素影响,产生复杂的动力学效应。近年来,连续型机器人的建模方法已从早期的运动学(例如:常曲率/分段常曲率法)或静力学(例如:Cosserat梁理论)向动力学发展。
图4 DAEs动力学模型:(a)杆或弹簧单元,(b)滑动绳索单元,(c1-c2)圆环单元
然而,现有的张拉整体结构建模多针对拓扑连接关系简单的构型,缺乏面向控制且便于硬件实现的通用建模方案。为解决这一问题,研究团队融合几何非线性位置有限元(PFEM)和多体动力学建模理论,提出了一种面向控制的TCR动力学建模方法。
如图4所示,团队首先基于PFEM,以全局坐标系下的空间节点位置坐标为基本未知量,推导各类构件的单元动力学列式;然后借鉴多体动力学理论,引入约束驱动;最终根据第二类Lagrange方程建立DAEs描述的TCR动力学模型。
这种建模方法具有三个优势:
1、直接获得全局坐标下的动力学方程,无需繁琐的坐标变换,可与测量设备直接对接
2、以滑动绳索的位移或速率为驱动输入量,可与电机直接对接
3、适用于不同拓扑构型的连续型机器人系统,具有良好通用性
▍末端位–姿协同跟踪的IOC控制器:算法创新是关键
有了准确的动力学模型,如何设计高效控制算法就成为关键。柔性连续型机器人属于高维强非线性系统,其末端运动控制的全局最优解难以获得。
为解决这一问题,研究团队借鉴瞬时最优控制(IOC)思想,将原本连续系统的全时域最优控制问题转化为一系列离散时间区段的次优控制问题,构建了一套连续型机器人末端位置与姿态轨迹协同跟踪控制的算法框架。
具体实现过程包括三步:首先采用广义-α方法建立受控DAEs动力学方程的数值离散格式,并通过牛顿迭代将跟踪控制问题转化为各迭代步的瞬时最优控制问题;然后考虑驱动长度或速率的安全阀值限制,即控制输入饱和的不等式约束,将原问题继续转化为规模仅为驱动绳索数目的线性互补问题(LCP);最后,通过求解该LCP便可获得满足输入饱和约束条件的控制律。
▍仿真与实验验证:场景测试展示实用价值
为验证所提方法的有效性,研究团队搭建了如图5所示的TCR闭环控制实验平台,包含视觉运动捕获系统、控制器计算单元和伺服电机驱动装置三个环节。
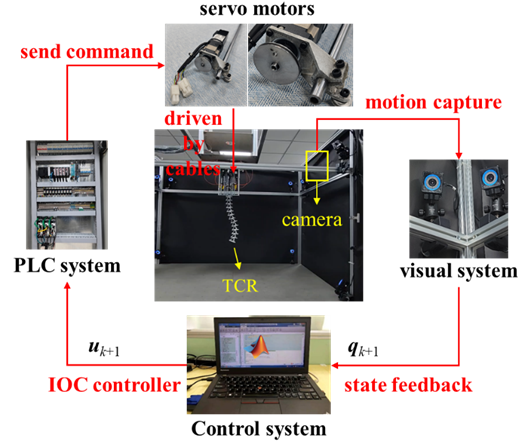
1. 动力学模型验证
首先验证模型的有效性。如图6所示,通过匀速率驱动TCR的主动滑动绳索,对比实验与仿真结果。数据显示,末端位置的平均绝对误差约为7.1mm,为TCR本体长度的1.10%,末端点位移的1.32%,表明所建立的数值模型具有准确性。
图6 模型验证:(a-b) 实验与仿真构型,(c) 末端轨迹
2. 末端位置轨迹跟踪控制
针对末端位置轨迹跟踪控制,以“I ♥ DUT”为目标轨迹进行测试,实现了复杂轨迹的跟踪控制,控制平均误差小于1cm。实验显示,TCR能完成这一包含直线、折线和圆弧的复杂轨迹跟踪任务。
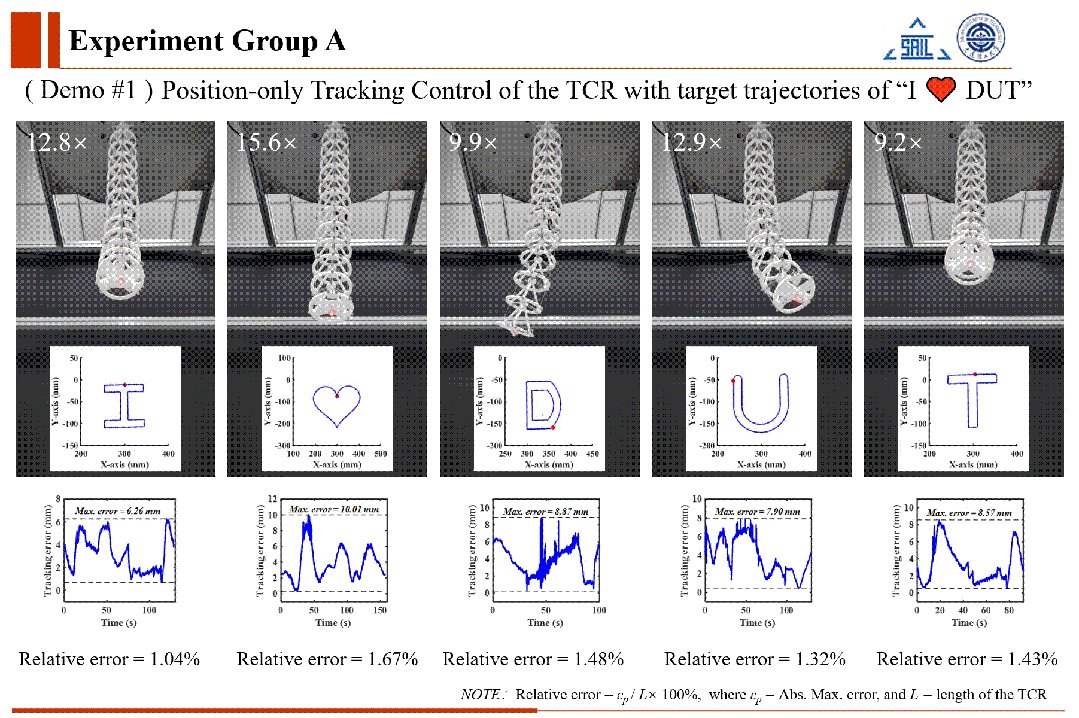
3. 末端位置与姿态轨迹的协同跟踪控制
更具挑战性的是末端位置–姿态协同跟踪控制测试。团队设计了三种不同目标轨迹任务:
Exp_1:以给定姿态跟踪圆柱螺旋曲线
Exp_2:以给定姿态跟踪圆锥台曲线
Exp_3:与水平面成55度角进行定点旋转
实验结果显示:三种任务的最大位置绝对误差分别为8.78mm、10.17mm和12.04mm,约为TCR本体长度的1.3%、1.5%和1.7%;末端姿态的方向角最大绝对误差控制在0.181rad以内。

研究团队还对比了基于动力学与基于静力学的控制效果差异。如图7所示,在快速运动场景(10秒内完成定点旋转)中,静力学控制方法很快就偏离目标轨迹并导致控制发散;而动力学控制方法则能稳定完成任务,末端位置X方向均方根误差仅为2.56mm,姿态角误差为2.98°。
图7 基于动力学与基于静力学的IOC控制器在不同跟踪速率下的控制结果对比:(a) 定点旋转位姿跟踪控制示意图,(b-d) 依次是跟踪时间为10s (快速)、45s (中速)和90s (慢速)的控制结果
这一对比显示了动力学控制在快速运动场景中的优势,特别是在需要同时控制位置和姿态的场合。
为展示该技术的应用价值,研究团队设计了两个典型应用场景:
场景一:TCR末端的激光瞄准穿越细长管道
图8 场景一,TCR激光瞄准穿越细长管道:(a) 激光器,(b) 管道左侧的位姿标记点,(c) 穿越管道的激光投影点
如图8所示,研究团队在TCR末端安装激光发射器,通过对末端位姿控制,使激光束穿过细长空心管道。实验过程是:先获取管道位置和姿态,以管道中心轴线为目标方向设定跟踪轨迹,然后通过控制使激光穿过管道投射到远端。
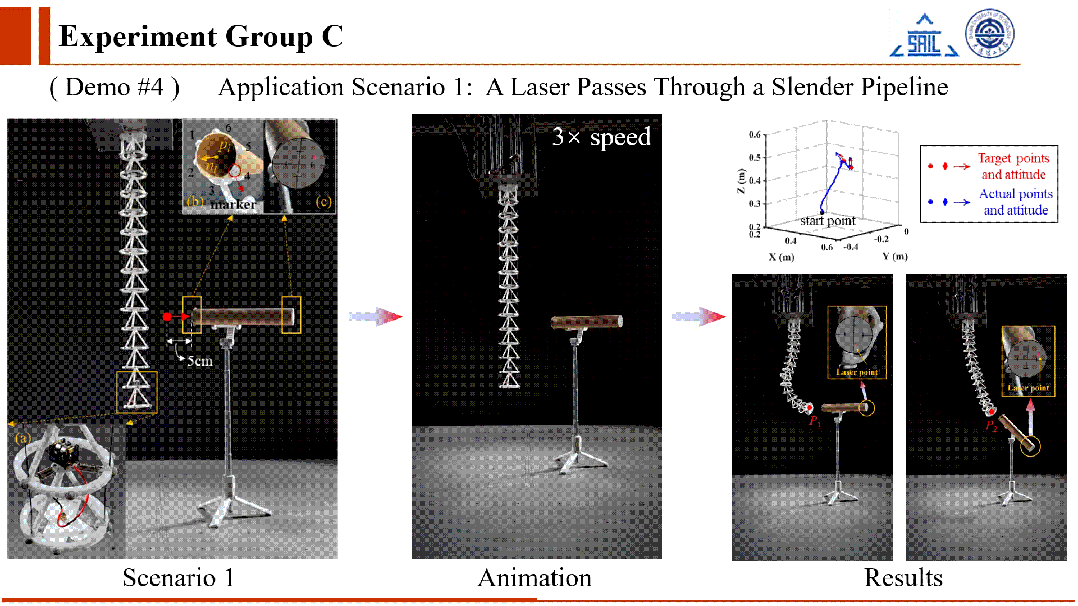
即使调整管道的位置和姿态,TCR仍能调整使激光穿过,这一能力对精密激光加工、焊接和检测等应用有参考价值。
场景二:TCR对结构狭小内部环境探测
图9 场景二:TCR利用进给孔对结构狭小内部环境探测
第二个场景更贴近实际应用。如图9所示,研究团队在TCR末端安装单目摄像头,通过狭窄入口探测盒子内部的随机放置物体。为对比位姿协同控制的效果,设计了两种探测策略,如图10所示:
图10 有无末端姿态控制的两种探测策略
策略一(仅位置控制):TCR末端只控制位置,通过不同位置的入口孔多次探测
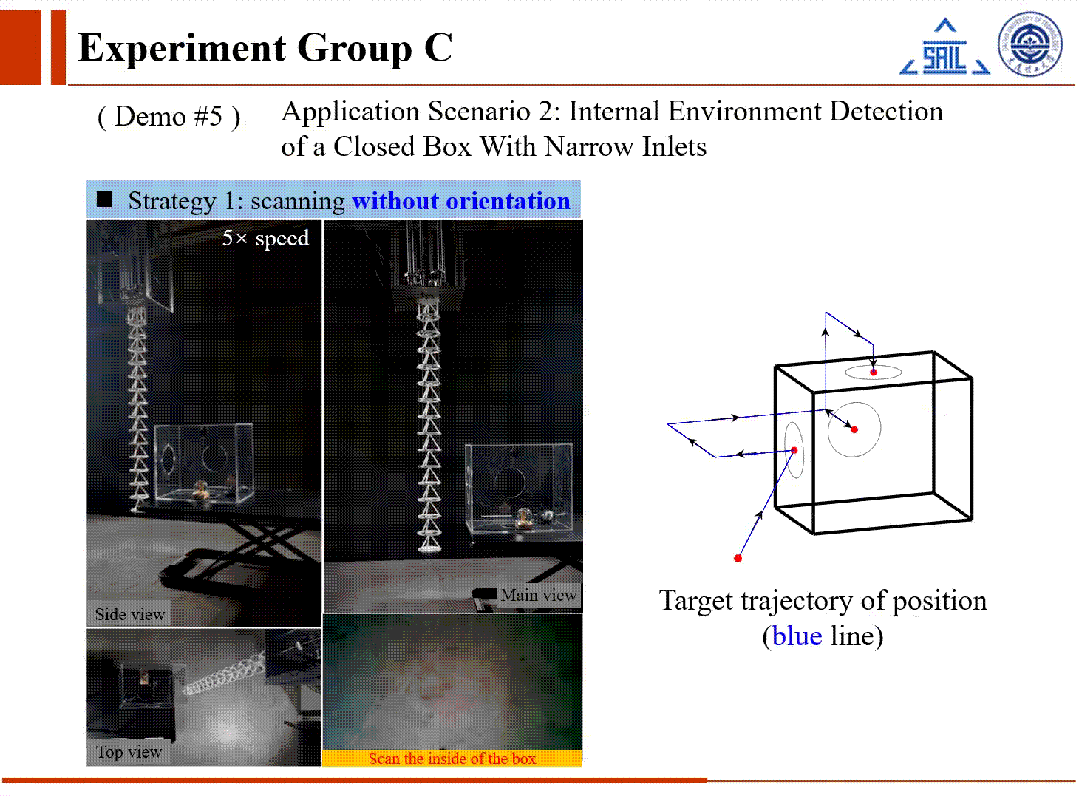
策略二(位置–姿态协同控制):TCR末端同时控制位置和姿态,通过单一入口孔扫视探测
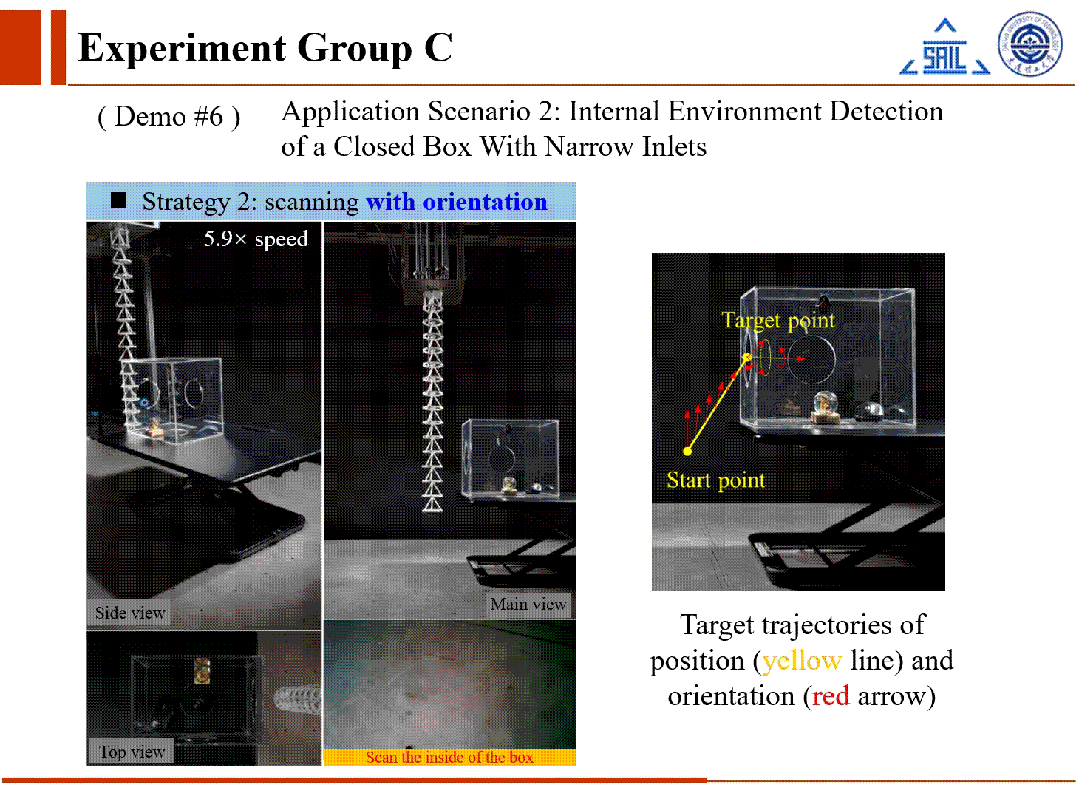
实验结果显示:采用策略一时,TCR发现1个目标物体且耗时183秒;采用策略二时,成功发现全部3个目标物体,且用时84秒,效率明显提高。
这一对比展示了末端位置–姿态协同控制在实际应用中的优势,说明该技术对提升狭小空间检测、内窥式检查等应用具有价值。
▍结语与展望
末端灵巧运动控制是连续型机器人应用发展的关键技术。本研究实现的TCR末端位置与姿态同步精准跟踪控制,相比传统仅控制位置的方法,可满足更多复杂场景需求。
所提出的IOC跟踪控制框架不仅适用于本研究中的TCR,还可拓展至其它连续型机器人,具有广泛适用性。该成果对推动连续型机器人控制体系发展具有重要理论价值和实践意义。
据悉,该团队未来将在此研究基础上更加深入系统地探索连续型机器人的动力学与控制相关理论,以突破连续型机器人具身智能感知、避障路径规划、振动抑制等关键技术挑战,最终实现重大装备狭小空间检测与柔顺装配等应用。
(文:机器人大讲堂)